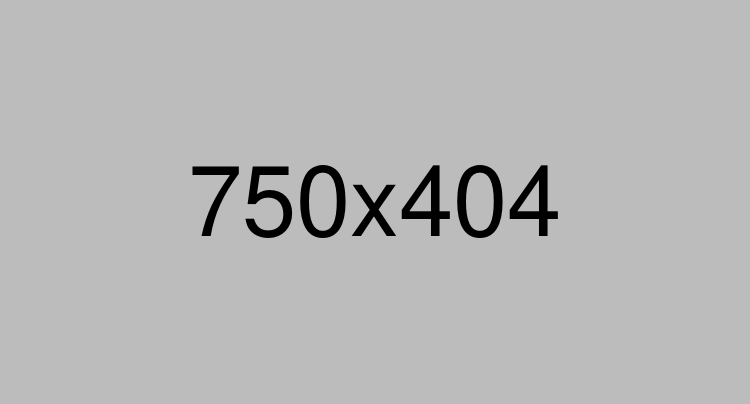
Ballmill
Tech India Engineers provides precision-engineered ballmills designed for high-efficiency industrial grinding. Our ballmills are built with advanced technology for optimal performance, durability, and energy efficiency. Suitable for various grinding applications, including cement, minerals, ceramics, and chemical processing, our ballmills ensure uniform particle size distribution with minimal wear and tear. Designed for both wet and dry grinding, they offer high-speed operations with reduced power consumption, making them a cost-effective solution for large-scale material processing. Whether you need a closed-circuit ballmill or an open-system grinding solution, we customize designs to fit your industry’s specific requirements.
Technical Specifications
- Grinding Capacity: 1 - 10 Tons per hour
- Material: Mild Steel / Stainless Steel
- Drive System: VFD-controlled motor
- Liner Material: High Manganese Steel
- Ball Mill Type: Open Circuit / Closed Circuit
- Grinding Media: Steel Balls / Ceramic Balls
- Operating Speed: 18 - 30 RPM (customizable)
- Motor Power: 50 HP - 500 HP
- Drum Diameter: 1.2m - 4m (customizable)
- Drum Length: 2m - 10m (customizable)
- Discharge Type: Overflow / Grate Discharge
- Lining Type: Rubber / High Manganese Steel / Alumina
- Control System: PLC-based automation available
- Cooling System: Water cooling / Air cooling options
- Energy Efficiency: Optimized motor with low power consumption
- Noise Level: < 85 dB (with noise reduction covers)
- Maintenance: Easy access for liner and media replacement
Key Features
- High-efficiency grinding with uniform particle size distribution
- Supports both wet and dry grinding applications
- Variable frequency drive (VFD) for speed control and energy savings
- Durable and long-lasting wear-resistant liners
- Customizable ballmill sizes for various industrial applications
- Low noise and vibration operation for improved workplace safety
- Optimized ball-to-material ratio for maximum efficiency
- Closed-circuit and open-circuit grinding options available
- Advanced PLC automation for process monitoring and control
- Minimal heat generation, reducing thermal stress on materials
- Heavy-duty gear drive for long-term operation
Applications
- Cement industry – Clinker grinding, raw material processing
- Ceramic industry – Fine grinding of ceramic powders and materials
- Mining industry – Processing of ores and minerals
- Paint industry – Mixing and grinding of pigments
- Pharmaceutical industry – Fine powder grinding for medical formulations
- Chemical industry – Grinding of resins, polymers, and other chemicals
- Glass industry – Grinding of silica and other raw materials
- Battery manufacturing – Processing of lithium and graphite materials
- Metal powder production – Fine grinding of ferrous and non-ferrous powders